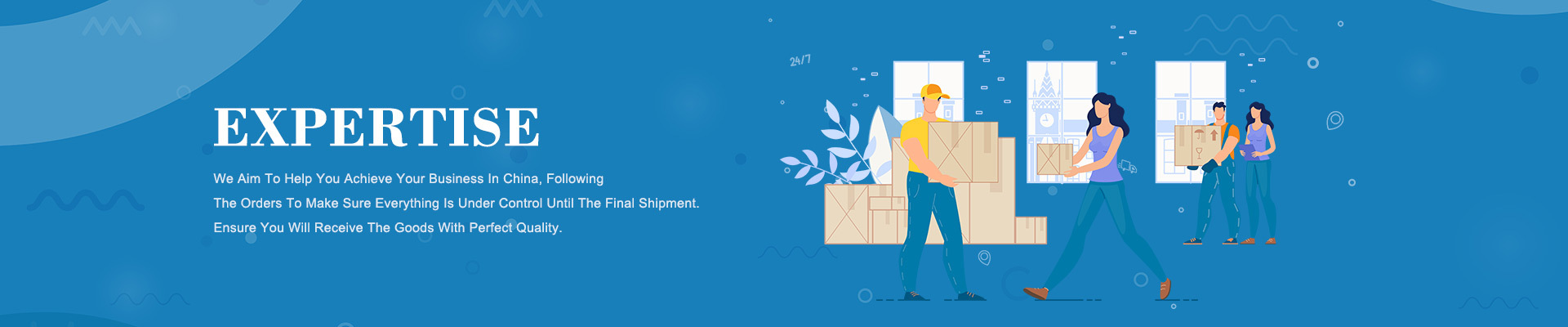
Production Follow-up
Manufacturing operations management is about making sure the final product matches the designs, and the production schedule is met.
Keep your production on point
Even if you have the best factory in the world, you could end up with a shipment of defective products if you don’t take precautions. What do you do if 20%, 50% or 90% of your product is unsellable? Can you get the factory to replace it? Can you wait months for the new shipment to arrive? In that case, what you really need is a time machine.
Production and operations management is absolutely essential to ensuring your product comes out right. Our inspectors are your on-the-ground representatives, eye catches and check your product’s quality run just as you would. They oversee the entire production process, so you can stay focused on building your brand at home.

Pre-production samples
Ahead of the full production run, our team visits the factory in-person to check pre-production samples, collect and review samples, conduct testing, and keep you constantly up to date,and deliver pre-production samples to you for check and sign if need it.

Start Production
Once you signed samples and manufacturing begins, we return at multiple points for quality inspection step by step during production, and send you a report with photos and videos. You track your production and make recommendations based on what’s happening in real time from your office (or home… or the beach).

Design & Functionality
By the time the assembly of your product is rolling, Our testers will for a design and functionality testing. Assuming that came out right, they get to work on completing the order. We’ll work with you to determine the possible points of failure so we can test them upon our return.

During production inspection
Once about 80% of the order is complete, we visually inspect it while taking photos and videos so you can see the results in real time. Then inspector use it how a customer would, checking that it functions as intended.
We go beyond the basics, down to the packaging. Most third-party testers won’t package a product up then drop it off a ladder. Ours will, because your product is going to have to survive some rough handling before it makes it to you then the customer. We send you videos of these tests so you can see for yourself. If we find defects at any point, we can work with the factory to resolve the issue and replace the damaged goods.

Final Quality Check
After the order is 100% complete, we check your products before you go through the expense of having them shipped. We get deep into the details––down to checking the spelling on all the packaging. If the production run passes quality standards, it’s good to go. If not, we sort it out.

A Necessary Precaution
Managing the manufacturing process during production is the only way to be certain your entire order comes together as planned. Evaluating and testing products early on lets us fix potential defects before your entire production run is complete.
Our inspectors follow AQL standards when determining whether the quality of the factory’s output is acceptable. These are the internationally accepted criteria, which means the manufacturer is obliged to comply whenever we demand they replace defective products and increase the overall quality of the production.

GYD Supply Source would be the key to improving your supply chain and win the competition in the future
Contact us
Add: No.350#301, Daluqian St. Guankou, Jimei, Xiamen 361023 China
Add: No.350#301, Daluqian St. Guankou, Jimei, Xiamen 361023 China
Copyright © 2024 GYD ( Xiamen ) Import & Export Co., Ltd | Powered by www.300.cn | Privacy Policy
COOKIES
Our website uses cookies and similar technologies to personalize the advertising shown to you and to help you get the best experience on our website. For more information, see our Privacy & Cookie Policy
COOKIES
Our website uses cookies and similar technologies to personalize the advertising shown to you and to help you get the best experience on our website. For more information, see our Privacy & Cookie Policy
These cookies are necessary for basic functions such as payment. Standard cookies cannot be turned off and do not store any of your information.
These cookies collect information, such as how many people are using our site or which pages are popular, to help us improve the customer experience. Turning these cookies off will mean we can't collect information to improve your experience.
These cookies enable the website to provide enhanced functionality and personalization. They may be set by us or by third-party providers whose services we have added to our pages. If you do not allow these cookies, some or all of these services may not function properly.
These cookies help us understand what you are interested in so that we can show you relevant advertising on other websites. Turning these cookies off will mean we are unable to show you any personalized advertising.
Sorry,当前栏目暂无内容!
您可以查看其他栏目或返回 首页
Sorry,The current column has no content!
You can view other columns or return Home