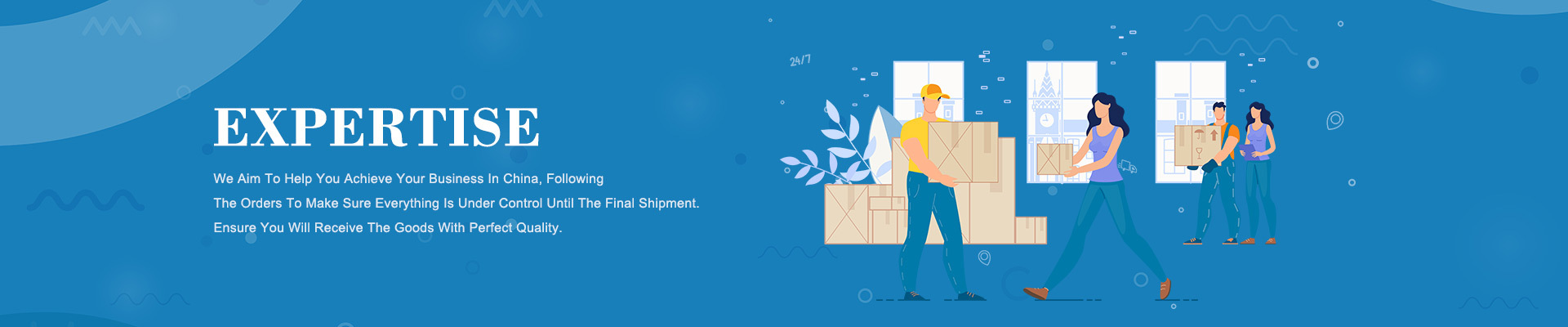
Die Casting
- Key Part in Process of Customized Product
What is Die Casting?
Die casting is a manufacturing process in which molten metal is forced into a mold cavity under high pressure. This mold cavity is typically made of steel and is referred to as a die. Once the metal solidifies, the die is opened, and the casting is ejected. Die casting is commonly used to produce metal parts with high accuracy, dimensional stability, and smooth surface finishes. The molds—tools or dies—are created using steel and specially designed for each project. This allows each component to be created with accuracy and repeatability. It is often used in the production of components for industries such as automotive, aerospace, and consumer electronics.
How to choose Die Casting materials for your products?
From zinc alloy, aluminum alloy, magnesium alloy, copper,stainless steel,lead,pewter and so on, the die casting process involves a lot of materials, what kind of products need what kind of materials? What should these materials pay attention to when making die casting? Need to have rich production experience and good product awareness.
In the structured product development process, the most important is the product implementation part, that is prototyping and engineering verification, both of which involve product engineering, and here will involve the die casting services, Die Casting is an important process of some hardware product development.


What We Do?
When you utilize GYD, we guide you through the entire process of manufacturing and communicate with you about the product you want to customize. Related to the details and problem points of the die casting process.
If you customized product involves die casting, we will help you select the die casting factory that is suitable for your product material. Will arrange tripartite communication to optimize the product design from the production point of view so as to meet your cost budget and factory mass production standards. Quote, negotiate the optimal price, develop quality inspection standards, GYD follow up the die casting process of product parts to ensure that mass-produced products are consistent with what you want to customize, we even help you improve your product design, if required.
What we do is to free your time, and spend more time on product function optimization and marketing.
Advantages of Die Casting
It is one of the most efficient and cost-effective methods of manufacturing metal parts and products of complex shapes and sizes in a variety of lightweight, high-strength materials. The production cycle is fairly simple, quick and easily repeatable. Hence, large quantities of the part or product can be manufactured in a matter of minutes and with a minimum requirement for post-production machining. What’s more, a variety of surface textures and finishes can be applied to the final product, such as anti-corrosion coatings and specialised, aesthetically pleasing finishes. This manufacturing method is also said to consume less energy and produce less material wastage than other metal shaping processes.
Disadvantages of Die Casting
Die casting is not suitable for low-volume production. Most manufacturers will quote a minimum order quantity (MOQ) because they make their profits from producing goods in bulk. The MOQ might vary depending on the raw material you request. Another factor to consider is tooling cost, which can run into the hundreds of thousands of dollars if you require a complex or large part to be cast. The time it takes to create your custom tool can also add to your lead time. Furthermore, if a tool requires modification after it has been made, this could reduce tool life and reliability down the line.
Other Tooling Limitations of Die Casting
The geometric complexity of the tool also affects cost and production speed. A simple tool can cost just a few hundred dollars to make whereas a larger or more intricate tool is more expensive to create. Similarly, a tool with greater geometric complexity will require a longer cooling time and, hence, a longer production cycle. This is why it is important to pay attention to the design of your product.
GYD Supply Source would be the key to improving your supply chain and win the competition in the future
Contact us
Add: No.350#301, Daluqian St. Guankou, Jimei, Xiamen 361023 China
Add: No.350#301, Daluqian St. Guankou, Jimei, Xiamen 361023 China
Copyright © 2024 GYD ( Xiamen ) Import & Export Co., Ltd | Powered by www.300.cn | Privacy Policy
COOKIES
Our website uses cookies and similar technologies to personalize the advertising shown to you and to help you get the best experience on our website. For more information, see our Privacy & Cookie Policy
COOKIES
Our website uses cookies and similar technologies to personalize the advertising shown to you and to help you get the best experience on our website. For more information, see our Privacy & Cookie Policy
These cookies are necessary for basic functions such as payment. Standard cookies cannot be turned off and do not store any of your information.
These cookies collect information, such as how many people are using our site or which pages are popular, to help us improve the customer experience. Turning these cookies off will mean we can't collect information to improve your experience.
These cookies enable the website to provide enhanced functionality and personalization. They may be set by us or by third-party providers whose services we have added to our pages. If you do not allow these cookies, some or all of these services may not function properly.
These cookies help us understand what you are interested in so that we can show you relevant advertising on other websites. Turning these cookies off will mean we are unable to show you any personalized advertising.
Sorry,当前栏目暂无内容!
您可以查看其他栏目或返回 首页
Sorry,The current column has no content!
You can view other columns or return Home