04
2025-03
Why are the injection molded products always defective
In the injection molding industry, product quality is one of the key factors that win the competitiveness of manufacturers.





Author:
In the injection molding industry, product quality is one of the key factors that win the competitiveness of manufacturers. However, many manufacturers often cause product defects during the production process, such as shrinkage, bubbles, flash, deformation and so on. Although the technicians continue to adjust the process parameters and optimize the mold design, the problem still exists. In fact, 90% of technicians overlook a crucial factor - material selection and process.
Let’s study the impact of materials on the quality of injection molded products and find out how scientific material management to reduce defects and improve the qualified rate of product.
Improper Material Selection: The root cause of defects
In the process of injection molding, the choice of material directly determines the physical properties, appearance quality and molding difficulty of the product. However, many factories tend to focus on only for the cost of material selection, while overlooking the applicability of materials. The following are some common defects caused by improper material selection.
Material shrinkage rate does not match
The shrinkage rate of different materials varies greatly. If the selected material shrinkage does not match the mold design, it will lead to product size deviation, shrinkage or deformation. For example, polypropylene (PP) has a higher shrinkage rate, while polycarbonate (PC) has a lower shrinkage rate. If the mold design does not consider the shrinkage characteristics of the material, the product is prone to dimensional instability or surface depression.
Materials illiquidity
The fluidity of the material directly affects the filling effect of injection molding. If the material flows poorly, it may result in insufficient filling, obvious weld marks, or poor surface gloss. For example, high-viscosity materials are difficult to fill completely in complex molds, especially in thin-walled areas, prone to short shots or bubbles.
The material has poor thermal stability
During the high temperature injection molding process, materials with poor thermal stability are prone to degradation, resulting in black spots, yellowing or strength reduction on the surface of the product. For example, some recycled materials or low-quality raw materials are easy to decompose at high temperatures, which not only affects the appearance of the product, but also may release harmful gases.
Material moisture content is too high
The water in the plastic particles will vaporize at high temperatures, resulting in bubbles or silver streaks inside the product. For example, if hygroscopic materials such as nylon (PA) are not sufficiently dried, there will be obvious silver wires or bubbles on the surface of the product after injection molding.
Improper material handling: defective catalyst
Even if the appropriate material is selected, it can still lead to product defects if it is processed not properly during handling. Here are some common material process problems:
Insufficient drying
Many plastic materials (such as ABS, PC, PA, etc.) are hygroscopic and must be fully dried before injection molding. If the drying temperature or time is insufficient, the moisture in the material will vaporize during the injection molding process, resulting in bubbles or surface silvers pattern inside the product. In addition, excessive drying may also lead to material degradation, affecting product performance.
The uneven mixing of the materials
In the production process, it is sometimes necessary to mix materials or additives of different colors. If the mixture is not uniform, it will lead to inconsistent product color or performance differences. For example, the uneven mixing of the masterbatch with the substrate can lead to color spots or streaks on the surface of the product.
Material contamination
During the storage and transportation of materials, if effective dust and moisture prevention measures are not taken, it may cause materials to be contaminated. For example, dust and metal chips or other impurities mixed into the material will cause defects on the surface of the product or less in internal strength.
Material aging
When plastic materials are stored or exposed to high temperature and high humidity for a long time, it will be aging, resulting in a decline in their physical properties. If the aging material is used for injection molding, the product is prone to problems such as embrittlement, cracking or poor surface gloss.
How to reduce defects through material management
To reduce the defects of injection molding products, it must start with the selection and treatment of materials and establish a scientific management system. Here are a few suggestions:
Select the right material according to the product requirements
In the selection of materials, it should not only consider the cost, but also consider the use of the product environment, performance requirements and molding process. For example, for products requiring high transparency, materials with excellent optical properties (such as PMMA) should be selected; For products that require high temperature resistance, materials with good thermal stability (such as PPS) should be selected.
Strict control of material quality
When purchasing materials, reputable suppliers should be selected, and technical data sheets (TDS) and inspection reports of materials should be requested. For critical products, third-party testing of the material is also possible to ensure that its performance meets the requirements.
Strengthen material drying management
For hygroscopic materials, drying must be carried out in strict accordance with process requirements. It is using professional drying equipment and checking the drying effect regularly. For different materials, different drying temperatures and times should be set to avoid excessive drying or insufficient drying.
The materials mixing processes optimize
In the mixing process, efficient mixing equipment should be used, and the mixing time and proportion should be strictly controlled. For masterbatches or additives, it is required to conduct small batch tests to ensure uniform mixing before mass production.
Preventing material contamination
Effective dustproof and moisture-proof measures should be taken during the storage and transportation of materials. For example, use airtight containers to store materials and avoid contact with dust or impurities. Install a magnetic filter at the feed port of the injection molding machine to prevent metal filing from mixing into the material.
Check material status regularly
For materials stored for a long time, their status should be checked regularly to avoid the use of aging materials. If the material performance is found to be reduced, it should be replaced or recycled in time.
Case study: How can Material Management Improve Product yield
When an injection molding factory produced a batch of highly transparent PC lampshades, it was found that silver patterns and bubbles often appeared on the surface of the product. After analysis, it is found that the problem lies in the drying process of the material. Due to the strong hygroscopic properties of PC materials, and the inaccurate temperature control of the drying equipment used by manufacturers, the drying of materials is insufficient. After improving the drying process and replacing the high-performance drying equipment, the product yield was increased from 70% to more than 95%.
Conclusion
The selection and deal with the materials is the most easily overlooked link in the injection molding process, but it is the key factor affecting product quality. Through scientific material management, manufacturers not only reduce product defects but also improve production efficiency and reduce production costs. High-quality products are the key to getting customers satisfaction.
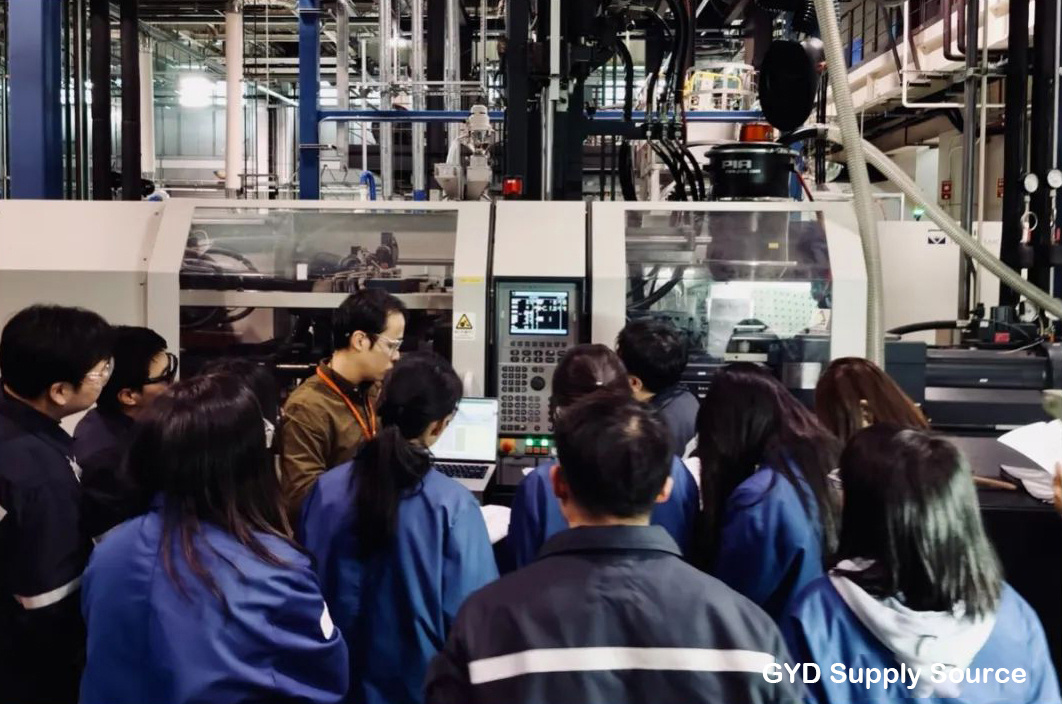
Related news
2025-03-27