19
2025-03
Common plastic product quality problems and solutions
Study about the immeasurable damage that these 20 common plastic product quality problems





Author:
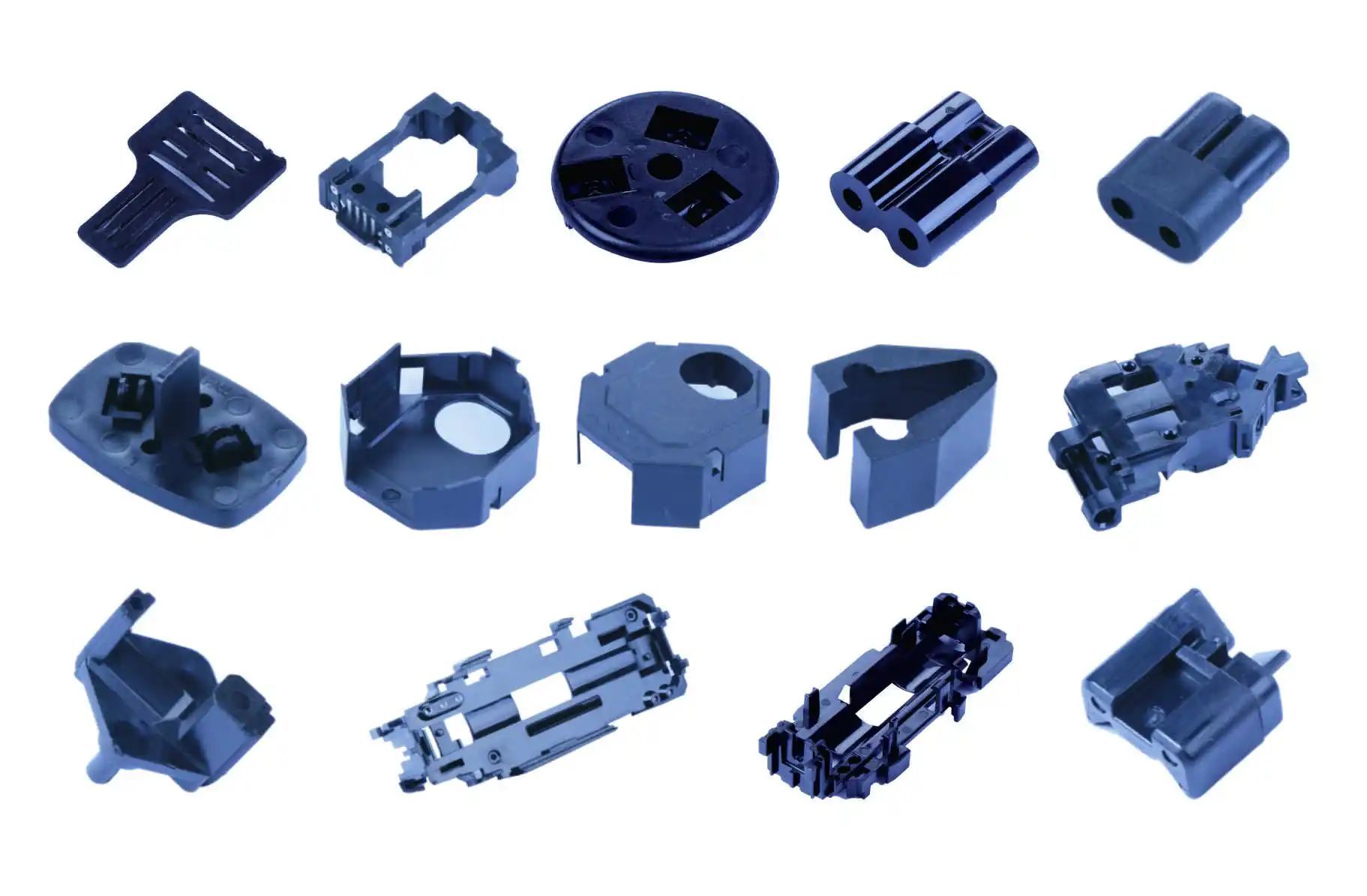
Let's analyze the occurrence and causes of misjudgment of the quality of plastic products. As we know, the defects of plastic products include: broken ejector pins, ejector marks (white spots), raised ejector marks, deformation, dimensional tolerance deviation, shrinkage, uneven glue flow, flower-like marks at the gate position, color mixing, miscellaneous spots, glue adhesion, whitening, cracking, pin deviation, ejector cracking, mold sticking, trapped gas, gas marks, scratches, burrs, and those caused by human factors such as scratches during processing, scraping, abrasion, compression deformation, fingerprints, oil stains that are not wiped off, residual plastic filaments, dust, etc.
Then, several factors that are most likely to cause us to make misjudgments are: broken ejector pins, ejector marks (white spots), raised ejector marks, deformation, dimensional tolerance deviation, shrinkage, uneven glue flow, flower-like marks at the gate position, color mixing, color difference, miscellaneous spots, glue adhesion, mold sticking, sand holes, whitening, cracking, pin deviation, trapped gas, gas marks, scratches, raised parts due to dragging, burrs, scratches during processing, scraping, abrasion. Now, let's analyze them one by one:
1. Broken ejector pins
The so-called broken ejector pin means that there is excessive plastic inside the hole of the column in the semi-finished product of the plastic product, or the depth is insufficient. This causes the screw to be unable to be screwed in place during assembly, or it is impossible to screw the screw in at all. In this case, we can determine that this part is NG and unacceptable. However, we need to pay attention to the situation of whether the screw can be screwed in place. Of course, if the hole of the column is completely blocked, it is scrapped. If the length of an M3 or M4 screw is shorter than the depth of the completely broken column, then as quality control personnel, our judgment is of course to accept it as OK. In another situation, if the depth of this part is required, and the customer receives the goods according to the depth requirement of the column of the part, and it does not affect the customer's assembly. Currently, what we need to do on-site is to first issue an abnormal document, immediately take isolation measures and mark the abnormal parts, and then notify the quality engineer, QA engineer or business engineer to report this situation. To seek a way to reduce product scrapping, the final acceptance, rejection, or the need for immediate mold repair should be decided after listening to the opinions of the relevant engineers.
2. Ejector Marks (White Spot)
Colleagues who have been engaged in the quality control of plastic products will not be unfamiliar with this. It is nothing more than the white circular marks left on the surface of the product after the ejector pins of the mold eject the product when the plastic product is demolded. We can directly determine it as NG or scrap at the first moment. However, when an ejector mark (white spots) appears, we need first to find out whether the plastic semi-finished product needs to be painted, what kind of paint is to be used and whether it can cover the mark. Secondly, we need to know which level of appearance the plastic part belongs to, how it is assembled, and whether it will be exposed in a prominent position on the surface of the finished product after assembly. We need to analyze these aspects before making a final judgment.
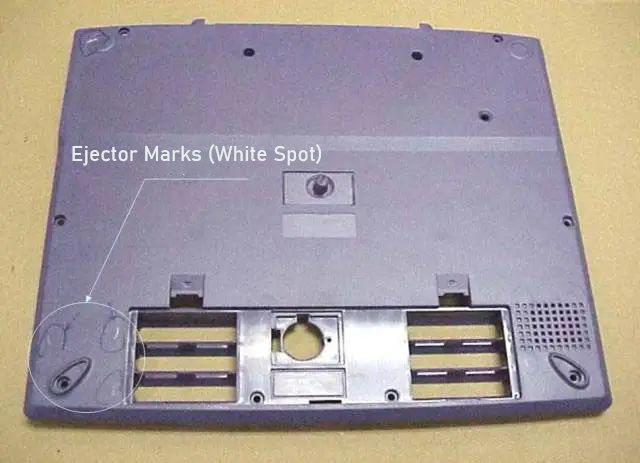
3. Raised Ejector Mark
That is, there are white circular marks on the surface of the plastic product, which are higher than the plane of the product, and there is a raised feeling when touched by hand. To be exact, it should be determined as NG and scrapped. However, we still need to figure out whether the product with the raised ejector mark really needs to be scrapped. We should make a comprehensive judgment from several aspects: 1. Whether the plastic semi-finished product is an internal component, and whether it will affect the use and function of the product after assembly. 2. Generally speaking, there should also be a certain degree for the raised ejector mark of the product. But if it is on the primary appearance surface, it is unacceptable. When it does not affect the assembly, function, appearance and dimensions of the entire product, as quality control personnel on-site, we still require the production department to improve the production process and then resume production. The products should be shipped after confirmation.
4. Deformation
Deformation can be divided into several situations, such as deformation caused by stacking before packaging, deformation caused by extrusion after packaging, and deformation that occurs right after the product is demolded during production. Firstly, there are plus or minus tolerances for product deformation. If there are such tolerances, the judgment should be made according to the plus or minus tolerances. If not, the judgment should be made based on whether it affects the assembly and the appearance of the finished product during the assembly process. In quality control during the manufacturing process, efforts should be made to ensure that the products are not stacked up in large quantities; and the packaging materials must also comply with the packaging material specifications stipulated by the PE engineering department. However, if the cause of the deformation during production is due to the unreasonable design of the mold or the deformation also occurs during the mold trial, then production should be carried out according to the sample. Because for any plastic product, it must first go through mold trial, sample approval, trial production, and then mass production, so there is no need to worry too much. Of course, the engineering research and development department of the company or the customer may also overlook this point, but our quality personnel will eye-catch the points and put forward suggestions during production.
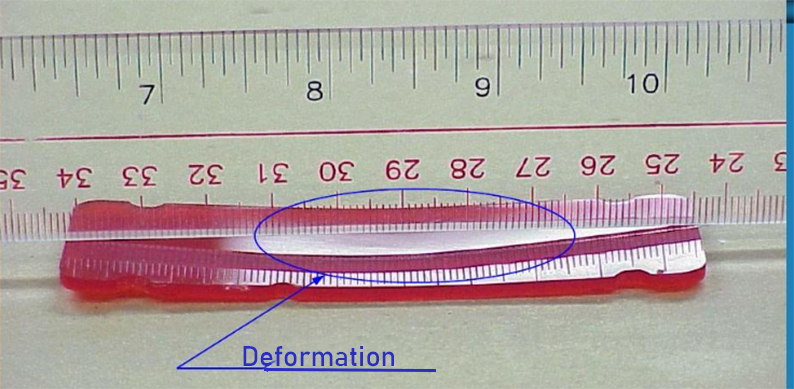
5. Dimensional tolerance deviation
The out-of-tolerance of dimensions is generally caused by several aspects:
(1) Have we accurately identified the measurement reference points indicated on the project-controlled drawings?
(2) Is the measuring tool expired, has its precision been compromised, are the scales unclear, or is it due to the fact that we haven't zeroed the measuring tool?
(3) Are there any errors in the measurement method and reading? For example, when measuring the length of the plastic semi-finished product shell with a caliper, have we ensured that the plastic part being measured is perpendicular and parallel to the caliper? Have we made sure that the value of the outer measurement point is the maximum value and the value of the inner measurement point is the minimum value? Have we applied too much force when taking the measurement data? If it is a metal part, is it because we clamped it too loosely? Have we carefully checked the minimum scale value of the measuring tool before taking the reading?
(4) Are both the measured position and the measuring tool we use accurate?
For example, when measuring the tolerance of the groove position of a column, we usually use a blade micrometer and measure the part that has been cut off with a hacksaw. So, are we using an ordinary micrometer for the measurement instead?
When measuring the depth of a blind hole, does the outer diameter of the pin gauge we use differ too much from the inner diameter of the blind hole? Have we ensured that the reading and data collection are done only after the pin gauge has been placed at the very bottom of the blind hole position? Of course, when we conduct precise measurements during the manufacturing process, if there are no problems with the measurement method, the controlled engineering drawings, and the measuring tools used, then the problem lies in the molding parameters and the mold. For instance, after the length and width dimensions of a plastic semi-finished product meet the requirements of the controlled engineering drawings during the molding process, if there is a serious scratching phenomenon on its secondary appearance surface (that is, the side surface of the product), it will affect the overall appearance of the finished product, which is unacceptable. Perhaps in the engineering field, a certain degree of dimensional out-of-tolerance may be allowed, but what we need to do is to issue an abnormal situation contact form to notify the relevant engineers to confirm it before making a final judgment. If the depth of the blind hole position is out of tolerance, it is a problem with the mold insert pin. However, if it does not affect the assembly, we also need to ask the relevant engineers to confirm it before making a final judgment!
6. Shrinkage
The shrinkage of plastic semi-finished products refers to the phenomenon of depressions appearing on the surface of the products, which is actually unacceptable. However, we will make a comprehensive judgment according to the following situations:
(1) In terms of engineering: Because if the surface of the plastic semi-finished product does not shrink, its dimensions will be out of tolerance and thus unacceptable.
(2) In terms of molding: It is possible that the molding parameters were not set properly during the shrinkage process, or it is caused by the inability of the performance of the injection molding machine to be controlled as required.
(3) In terms of the mold: It may be caused by the fact that the plastic part of the semi-finished product is too thick at a certain position. It is also possible that when the product is demolded, the plastic part may be pulled into a depression, or if there is no shrinkage, scratching may occur on the secondary appearance surface.
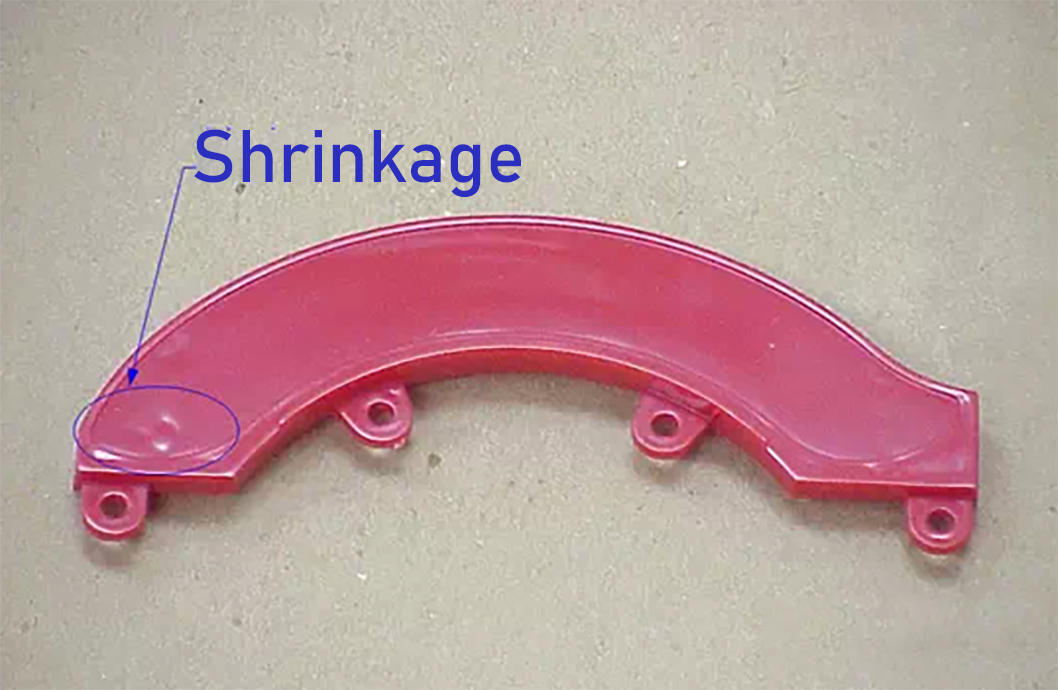
Once any of the above three situations occurs, the on-site quality control personnel should immediately notify the relevant staff in the production department, such as the production foreman, production machine adjustment technician, or senior production technician, etc. Then, an abnormal information form should be issued and fed back to the relevant engineers for comprehensive judgment, and then the action of acceptance or rejection can be taken.
7. Uneven glue flow
As our peers all know, uneven glue flow means that there is a lack of glue in the plastic semi-finished product. Then, is all the lack of glue considered as a rejection (NG) and the product should be scrapped? Do we need to adjust the molding parameters for all the plastic semi-finished products with uneven glue flow? The answer is: not all cases of uneven glue flow require adjusting the molding parameters or lead to scrapping! Whether the molding parameters need to be adjusted for uneven glue flow, we need to understand it fundamentally.
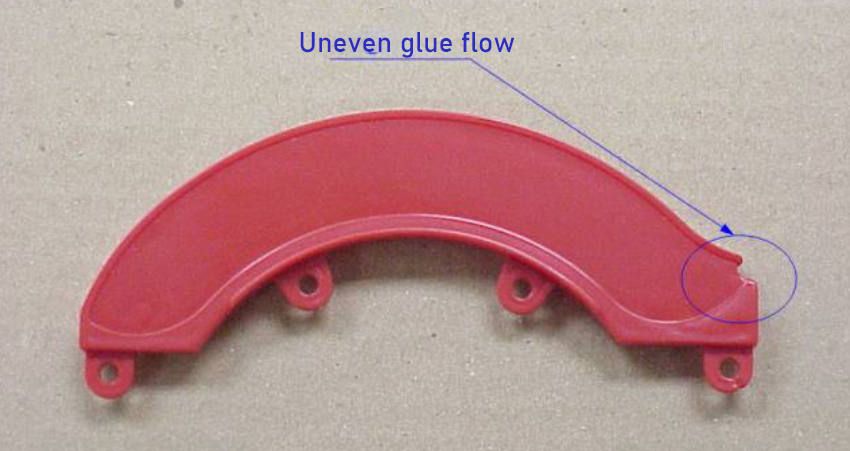
(1) Is the uneven glue flow caused by the improper venting of the mold?
(2) Is it caused by the fact that the plastic part of this semi-finished product is too thin?
(3) Although there is uneven glue flow, does it affect the assembly, the usage function, and the appearance of the finished product after assembly?
(4) Is it due to the inability to control the performance of the machine?
For the first three situations, we need to confirm them with reference to the customer-approved sample, the limit sample, and the AOD board! For the last situation, we directly determine it as NG, but it is necessary to make a comprehensive judgment by combining it with the first three situations. The reason is very simple. Because the quality status of the same set of molds produced on different machines may be different, or there have been similar quality situations in the past. At the same time, we also confirm it with the help of the quality defect ledger! If necessary, we can notify the relevant engineers to provide technical assistance. Our peers also know that, inevitably, such situations may occur when using the same mold and the same machine but different materials. Be careful!
8. Flower-like marks at the gate position
The gate is the position of the glue inlet. Once flash marks occur, they will appear on the surface of the product, which can be either obvious or unobvious. Similarly, when it comes to the quality control during the manufacturing process, we should not be too hasty in making judgments. Just because flash marks appear doesn't mean the product is immediately rejected (NG). What we need to do is to make a correct judgment. Of course, once such a situation occurs, no matter what, production should not continue. We need to immediately adjust the molding parameters or check if there is a problem with the mold. At the same time, when the relevant personnel in charge of quality control during the manufacturing process are unsure, they should notify the relevant quality assistant engineers or relevant engineering management personnel for confirmation.
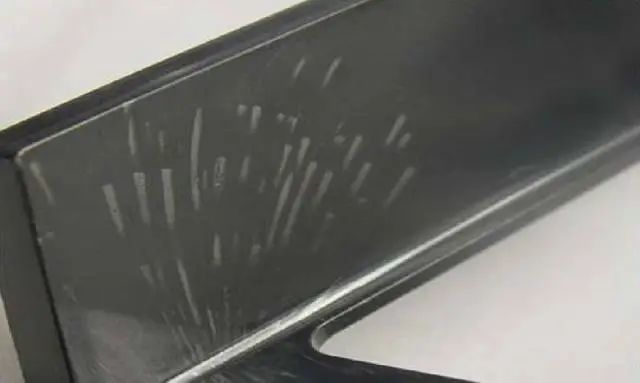
9. Color mixing and color difference
Color mixing and color difference are all too familiar to us when it comes to quality control during the manufacturing process. At the same time, they are also an important factor contributing to the increase in production costs. The plastic semi-finished products most prone to color mixing are those produced by mixing color powder with raw materials. First of all, in order to determine whether the color mixing is a rejection (NG), we need to figure out the customer's acceptance criteria, whether the raw materials received each time are from the same supplier, the ratio of the color powder to the raw materials, and also pay attention to whether the equipment of this machine is suitable for producing the plastic semi-finished products made by mixing this color powder with the raw materials.
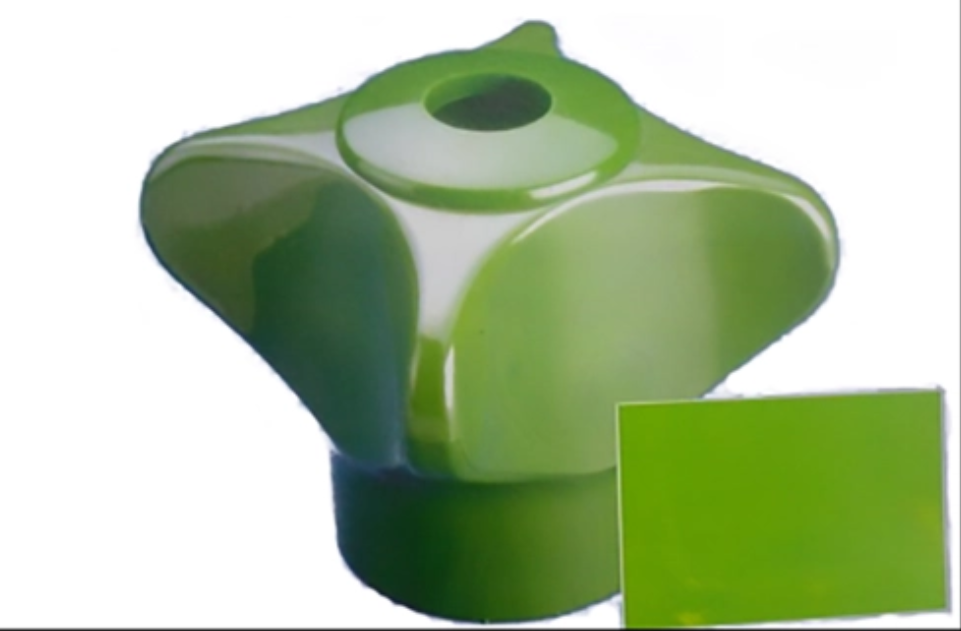
We also know that it is inevitable that there will be color differences when the raw materials supplied by different suppliers are used together with different color powders. In the past, we had always complained by customers about why the colors were not consistent for each batch of products. Upon careful investigation, it is due to our excessive sensitivity to production costs. If we use pelletized materials for production, we think that the cost is higher than that of mixing color powder with raw materials. However, the rejection rate due to color mixing and color differences is low when using pelletized materials, and the color is stable. On the contrary, the rejection rate is high when mixing color powder with raw materials. According to incomplete statistics, the rejection rate of products produced by mixing color powder with raw materials is as high as over 20%. It is obvious which one has a higher cost in the long run. In terms of quality control during the manufacturing process, we can ask quality engineering and business engineering to provide technical support. For example, color panels, color difference values, color difference meters, or color matching light source boxes, etc. I think that for plastic semi-finished products with color mixing in the quality control during the manufacturing process, it is best to keep the limit boards, AOD boards, and NG sample boards signed by relevant engineers for a long time. Those with discrepancies must be sealed up and should not be referred to!!!
10. Miscellaneous spots
During the manufacturing process, our peers often say that there are foreign objects or black spots on the primary appearance surface of plastic semi-finished products. Here, I will collectively refer to them as miscellaneous spots!
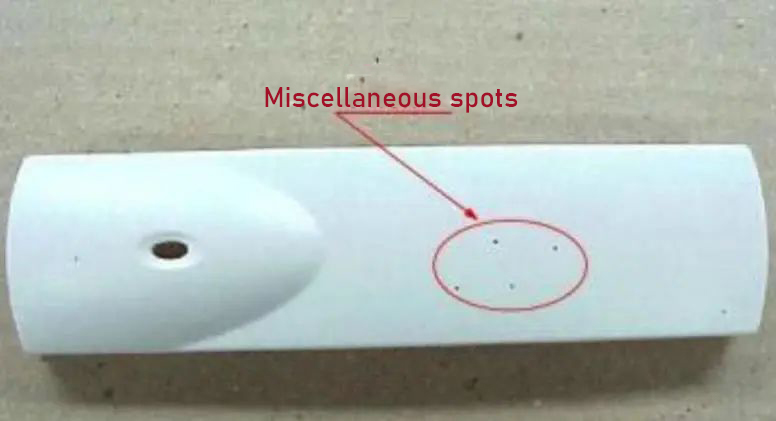
Under different customer requirements, some miscellaneous spots on plastic semi-finished products can be accepted, while others need to be scrapped! According to the actual production situation, customers will also provide corresponding technical assistance. For example, they will provide foreign object films. However, this is often not enough. We usually know that some foreign objects seem to exceed the standard.
For instance, customers like Toshiba and Apple require that the diameter of foreign objects should be 0.1mm. But if the actual diameter of a foreign object is 0.15mm, and it is located 0.2mm deep inside the plastic layer of the primary appearance surface of the plastic semi-finished product, and it appears blurry. When viewed at a distance of 60cm to 45cm under a 40W or 60W standard fluorescent light source and blinking the eyes 5 times, it may not be clearly visible. In this case, the product can be accepted.
There is another situation regarding the distance requirement between two points. If the required distance between two foreign objects is 50 to 45mm, two points with a diameter of ≤0.15mm are acceptable. But what if the two blurry small points are less than 50mm or less than 45mm apart? Should it be determined as NG? We need the engineering department to provide the answer. I think that if it is not clearly visible even after blinking the eyes 5 times under a 40W or 60W standard fluorescent light source, it can also be accepted.
11. Glue Adhesion and Mold Sticking
The adhesion of plastic semi-finished products to the glue and the adhesion to the mold are two different concepts. Adhesion to glue refers to the appearance of irregular scar-like concave marks on the primary and secondary appearance surfaces of the plastic semi-finished products. Adhesion to the mold means that the screw posts, positioning posts, and positioning ribs of the plastic semi-finished products are completely stuck in the mold cavity. However, in the case of adhesion to the glue, it depends on the degree. It is completely unacceptable and classified as NG, and adhesion to the mold is also considered NG. If we fail to detect such situations during the quality control of the manufacturing process, it only shows that we have made a low-level mistake.
12. Sand holes
In plastic semi-finished products, some sand holes have nothing to do with the mold, while others are closely related to the mold itself. They can also appear on the surface or side of the plastic semi-finished products. If it is not a problem with the mold's own material, then it depends on the size, and it may be directly classified as NG. Why do we say so? Firstly, we need to check whether the customer has ever complained about such problems with the plastic semi-finished products. Secondly, after the plastic semi-finished products with sand holes are made into finished products, it will affect the appearance. The most important thing is to consider the customers’ requirements. If the foreign object is very small, for example, if its size is ≤0.1mm or ≤0.15mm and the depth is within 0.1mm, a small amount of it should be acceptable. However, improvement is required during production. If it is caused by the problem of the mold's own material, then immediately issue abnormal information feedback to the relevant engineers for follow-up improvement, seek the best treatment plan, and make a final judgment.
13. Whitening and Cracking
Some of our peers who are currently engaged in the quality control of plastic products have been doing this for several years, and they must have been complained about by customers regarding the abnormalities of whitening and cracking, right? Now, let's first look at where whitening and cracking generally occur in plastic semi-finished products. They occur in the following aspects:
(1) At the rib positions of the product.
(2) At the insert positions of the product (that is, the side surface).
(3) At the root of the columns.
(4) At the buckle positions.
In fact, when comparing the two, the situation of whitening is not as serious as that of cracking. Whitening also varies in degree. For major customers like Kyocera, they require that for us suppliers, whitening is not acceptable regardless of the degree, as it will affect the service life of the assembled finished product. As we all know, Toshiba and Kyocera are large Japanese multinational companies listed among the Fortune Global 500. Therefore, if there is whitening in the plastic semi-finished products, they will determine it as NG. However, we will also observe that if the whitening of plastic semi-finished products is caused by the problem of the mold slide positions, the rib positions of the plastic semi-finished products are not deformed, we will process and ship the products. Similarly, it will not affect the service life of the finished assembled product. But cracking means the product should be scrapped! At the insert positions, the root of the columns, and the buckle positions, as long as there is no cracking, and there is only whitening which does not affect the assembly and the function of screwing and also does not affect the service life of the product, it is also possible to process and ship the products. For the specific situation, we also need to consider the customer's requirements. During production, we will also issue abnormal reports to inform the relevant engineers to follow up and handle the situation.
14. Pin Deviation
Here, when we talk about pin deviation, it means that the ejector pin in the mold is skewed, resulting in the screw hole of the plastic semi-finished product being larger. When the aperture size is too large, during the product assembly process, the screw will slip when being screwed in, which seriously affects the function and usability of the product. Colleagues in charge of quality control of the dimensions during the manufacturing process should take note that the aperture size must be controlled within the tolerance range. If the aperture size is large, it is necessary to inform senior management at or above the level of quality assistant engineer for judgment and tracking and seek the best quality judgment before shipping the products.
15. Trapped gas
Trapped gas in plastic semi-finished products means that this situation occurs due to the improper exhaust system in the mold cavity. The phenomena of trapped gas in plastic semi-finished products are as follows:
(1) Lack of glue beside the rib position.
(2) There is a burnt appearance at a certain place beside the rib position.
(3) The glue fails to fully fill the buckle position.
(4) There is a forked clamping line at a certain place on the secondary appearance surface.
(5) There is a white-burnt or black-burnt appearance at the semi-circular rib position.
(6) The glue fails to fully fill the positioning post.
In summary, we can identify the following problems: lack of glue at the rib position, burnt rib position, white-burnt and black-burnt rib position, lack of glue at the buckle position, clamping line, and lack of glue at the positioning post. Can all of these be determined as NG? The answer depends on the situation. Firstly, we need to pay attention to whether there have been any previous complaints about these types of abnormalities and whether their degrees are the same. Then, in our sample management, do we have limit samples, AOD boards, and engineering confirmation samples for lack of glue at the rib position, burnt rib position, white-burnt and black-burnt rib position, lack of glue at the buckle position, clamping line, and lack of glue at the positioning post? Also, are there any similar abnormalities on the customer-approved board? If there are such samples, the quality control personnel during the manufacturing process should strictly follow these samples to make acceptance and rejection decisions. If not, the quality control personnel during the manufacturing process should issue quality abnormality documents immediately, contact the relevant engineering management personnel for comprehensive judgment, and then make a final decision.
16. Gas marks
The so-called gas marks refer to a small piece of foggy and matte substance in a circular or elliptical shape, which appears on the primary appearance surface or the secondary appearance surface corresponding to the position of the glue inlet of the plastic semi-finished product. This situation is also closely related to the size of the glue inlet of the mold and the molding parameters. If the gas marks are obvious on both the primary appearance surface and the secondary appearance surface, it is necessary to carefully check the customer-approved sample before determining whether it is NG or OK. It is required to improve the production process and then resume production. However, if it is caused by the unreasonable design of the mold itself rather than the problem of the molding parameters, and we ask the production department to adjust the machine, the subsequent work will be rather troublesome.
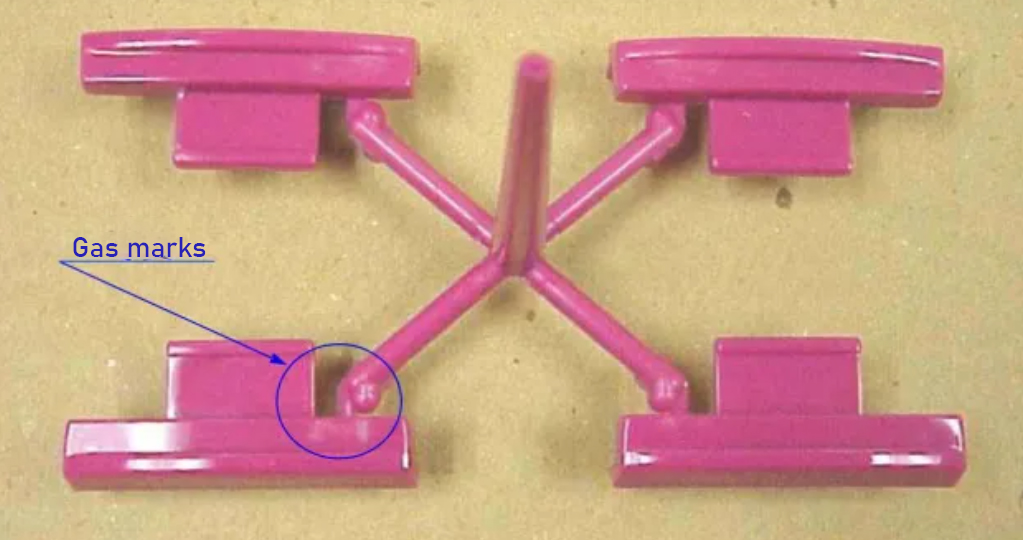
Those who have been in the same line of work are very clear about the term "gain and loss", that is, where there is gain, there must be loss, and where there is loss, there must be gain. When you want to adjust the gas marks, the production technician will increase the injection speed to get rid of the gas marks. However, when doing so, the clamping line at a certain part of the semi-finished plastic product may become more obvious than before, and it may not match the sample. Here, I suggest that the quality control personnel during the manufacturing process should check the sample first and then decide whether to let the production technician adjust the molding parameters. The specific handling method is to first issue a quality abnormal information feedback form to the senior production technician to seek the best solution and let them assist in handling the quality abnormalities. At the same time, we should also notify the relevant engineering management personnel to provide technical support to the quality control department!
17. Scratches and raised parts caused by dragging
Let's first analyze where the scratches and raised parts of plastic products are generally more likely to occur:
(1) The textured surface of the secondary appearance surface or the side surface.
(2) Insert positions and inserted pin positions.
(3) Perforation positions.
(4) Inclined ejector pin positions.
(5) Core-pulling positions.
(6) Mold slide positions.
(7) The raised marking positions on the primary appearance surface.
According to the differences in products and customer requirements, when there are scratches but no raised parts on a certain plastic part, we usually require the production department to improve the production process. There is an exception here: when the entire textured surface of the secondary appearance surface or the side surface is scratched. If our quality control personnel ask the production technician to make improvements, it will affect the length dimension of the entire part and cause a shrinkage phenomenon in appearance. Here, I still suggest that our quality control personnel should carefully check the sample, or the limit board for scratches, or the AOD sample, and then suggest that the production technician make improvements. Otherwise, new problems will arise and need to be confirmed. Generally, the sample management department of the quality department will keep relevant samples of plastic parts with scratched texture surfaces. We should look first and then conclude whether it is really necessary to make improvements. Of course, there is also a situation where there is a single scratch with a relatively deep scratch mark, and in this case, the mold needs to be polished. At this time, we need to consider whether the produced part can be shipped. However, I think if it cannot be shipped, it can be directly determined as NG. But we still need to notify the quality assistant engineer or the quality engineer to seek a judgment. If there are slight scratches at the insert positions, inserted pin positions, perforation positions, inclined ejector pin positions, core-pulling positions, mold slide positions, and the raised marking positions on the primary appearance surface, as long as the plastic powder caused by the scratches is wiped clean with a white cloth, it can be accepted, but the production department is required to make immediate improvements and then resume production. If the improvement cannot be achieved, an abnormality should be issued to notify the relevant engineers to follow up and improve such quality abnormalities.
18. Burrs
When it comes to the burrs of plastic parts, I'd like to say something. What kind of concept do we have about the requirements for burrs?
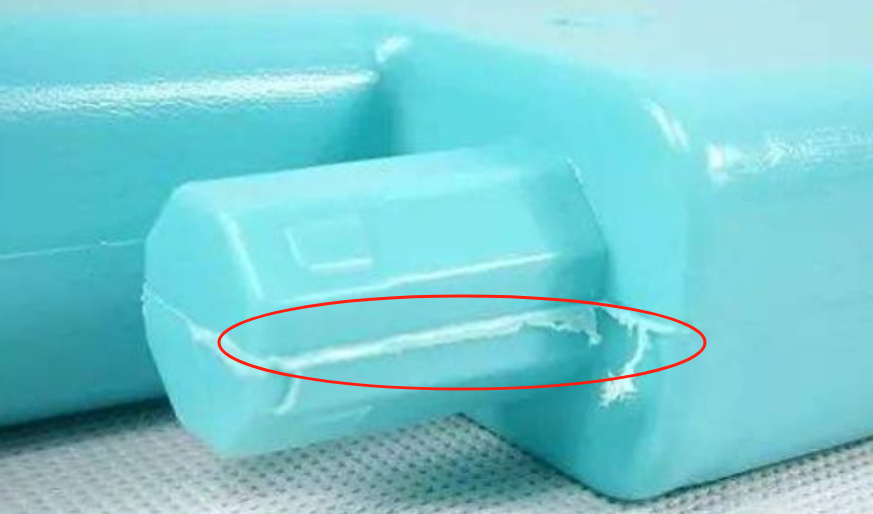
Some customers have the following requirements for the burrs of plastic parts. Take two major Fortune Global 500 customers, Toshiba and Kyocera, as examples. They consider it acceptable if the burrs on the periphery of the plastic semi-finished products supplied by us suppliers are ≤ 0.15mm. Today, with the maturity of the plastics industry, we also need to consider the production costs in production. If all plastic parts with burrs are not allowed and need to be processed, our company will have to spend a large amount of manpower on processing the burrs. Moreover, the processing of burrs will also bring many uncontrollable factors to our on-site quality control. For example, if there are phenomena such as bruising or deformation caused by burr processing and these defective products flow into the qualified products, it will lead to a second complaint! Although the defective rate is only about 5%, if calculated in PPM, it will be a very high defective rate. So, where will the burrs of a plastic part occur? The most likely place for burrs to occur is at the parting surface of the front and rear molds. For example: hole positions, through-bump positions, slide positions, buckle positions, inclined ejector pin positions, ejector sleeve pin positions and other places.
The following are the factors that cause the plastic semi-finished products to have burrs:
(1) The molding parameters of the machine are not adjusted stably.
(2) It is caused by the large opening of the mold exhaust groove.
(3) It is caused by the looseness of the ejector sleeve pin.
(4) It is caused by the looseness of the ejector pin.
(5) It is caused by the collision damage of the insert position.
The above five types of abnormalities that lead to the burrs of plastic parts are not allowed. Especially the first type of abnormality, in severe cases, it will cause the dimensions of the plastic semi-finished products to be NG and unable to be used. For the burrs caused by the second, third, fourth, and fifth types of abnormalities, processing is still required. After this order is completed, the on-site quality control personnel should promptly notify the senior production technician to follow up and optimize such burr phenomena.
19. Scratches during processing
If there is processing of burrs on plastic parts, the abnormality of scratching may occur. If the burrs on the secondary appearance surface are processed and there is scratching, but it does not damage the textured surface of the part and has no impact on the assembly clearance, it can be accepted. However, if the part is completely an internal component, a little scratching that does not affect the assembly is also acceptable! But some customers also have certain requirements for the concept of scratching on plastic semi-finished products. It is necessary to make a comprehensive judgment according to the customer's acceptance standards before shipping the products.
20. Scratches and abrasions
Scratches and abrasions are not acceptable in quality control during the manufacturing process, especially for products produced by some polished molds. Operators are required not to pile up too many parts on the desktop during operation, and anti-scratch and anti-abrasion rubber pads should be placed on the workbench to prevent the plastic parts from being scratched or abraded.
Another situation that the quality control personnel during our manufacturing process should pay attention to is that when such products need to be reworked due to other factors, they should be vigilant about scratches and abrasions. I suggest that for such products, if there are no extremely serious defects among the qualified products, operators should not be required to rework them to reduce the number of defective products with scratches and abrasions. It is better to make a little more effort to increase the inspection frequency and go to the machine tabletop more often to control other defective products from flowing into the qualified products, so as to reduce rework.
Finally, we also understand that when it comes to work of quality control during the manufacturing process, we should not easily say that a product is OK, nor should we casually determine it as NG. Moreover, we should not casually ask the production department to adjust the molding parameters at will to improve the existing quality situation. Instead, we should consult the relevant engineering management personnel more often, check the samples, AOD boards, engineering boards, and customer-approved engineering samples more carefully. What's more, we should make fewer judgments and run more errands to seek the best answers from the engineering side. In this way, we can reduce our own misjudgment rate and improve our work efficiency and professional skills.
Related news
2025-03-27